The Power of Total Productive Maintenance (TPM) with VA Innovation Ltd
Enhancing Equipment Efficiency and Productivity Through Comprehensive Maintenance Strategies
In the competitive world of manufacturing and production, maintaining optimal equipment performance and minimising downtime is crucial for success. One of the most effective strategies to achieve this is through Total Productive Maintenance (TPM).
Total Productive Maintenance (TPM) is more than just a maintenance strategy; it's a holistic approach designed to improve the overall efficiency and effectiveness of manufacturing equipment. By engaging all employees in proactive maintenance activities, TPM aims to maximise equipment uptime, enhance productivity, and reduce operational costs. This comprehensive methodology integrates maintenance into daily operations and promotes a culture of continuous improvement.
In this article, we delve into the key objectives and core principles of TPM, exploring how it empowers organisations to achieve maximum equipment availability, enhance performance, increase product quality, and reduce maintenance costs. Additionally, we will highlight various use cases across different industries, demonstrating how TPM can be applied to transform operations and drive business success.
Brief History of Total Productive Maintenance (TPM)
Total Productive Maintenance (TPM) has its roots in the evolution of maintenance practices and the pursuit of operational excellence within manufacturing industries. The history of TPM can be traced back to the mid-20th century and is closely associated with the development of quality and efficiency methodologies in Japan.
1950s-1960s: Origins and Development
The origins of TPM can be linked to the maintenance practices in Japan during the 1950s and 1960s. Post-World War II, Japanese industries were focused on rebuilding and enhancing their manufacturing capabilities. During this period, preventive maintenance practices began to take shape, emphasising the importance of maintaining equipment to prevent unexpected breakdowns.
Nippondenso, a Toyota Group company, played a pivotal role in the development of TPM.
In the early 1960s, Nippondenso implemented a proactive approach to maintenance, where operators were trained to perform routine maintenance tasks. This early form of TPM was aimed at reducing equipment downtime and improving productivity.
1970s: Formalisation and Expansion
The term "Total Productive Maintenance" was officially introduced in the 1970s by Seiichi Nakajima, a prominent figure in the field of maintenance and productivity. Nakajima, often referred to as the father of TPM, worked to formalise the concept and promote its adoption across various industries.
In 1971, the Japan Institute of Plant Maintenance (JIPM) was established, further advancing the principles of TPM. JIPM developed a structured framework for TPM implementation, emphasising the involvement of all employees in maintenance activities and the importance of continuous improvement.
1980s-1990s: Global Adoption
Throughout the 1980s and 1990s, TPM gained international recognition and adoption. Western companies began to take notice of the successes achieved by Japanese manufacturers using TPM. Organisations worldwide started to implement TPM practices to enhance their operational efficiency and competitiveness.
During this period, TPM evolved to encompass various aspects of manufacturing and production, including quality maintenance, early equipment management, and focused improvement. The eight pillars of TPM were established, providing a comprehensive framework for implementation.
2000s-Present: Evolution and Integration
In the 21st century, TPM has continued to evolve and integrate with other management methodologies such as Lean Manufacturing and Six Sigma. The integration of TPM with these approaches has further enhanced its effectiveness in driving operational excellence and continuous improvement.
Today, TPM is widely recognised as a key strategy for maximising equipment efficiency, reducing maintenance costs, and improving overall productivity. It is applied across diverse industries, including automotive, food and beverage, pharmaceuticals, utilities, and more.
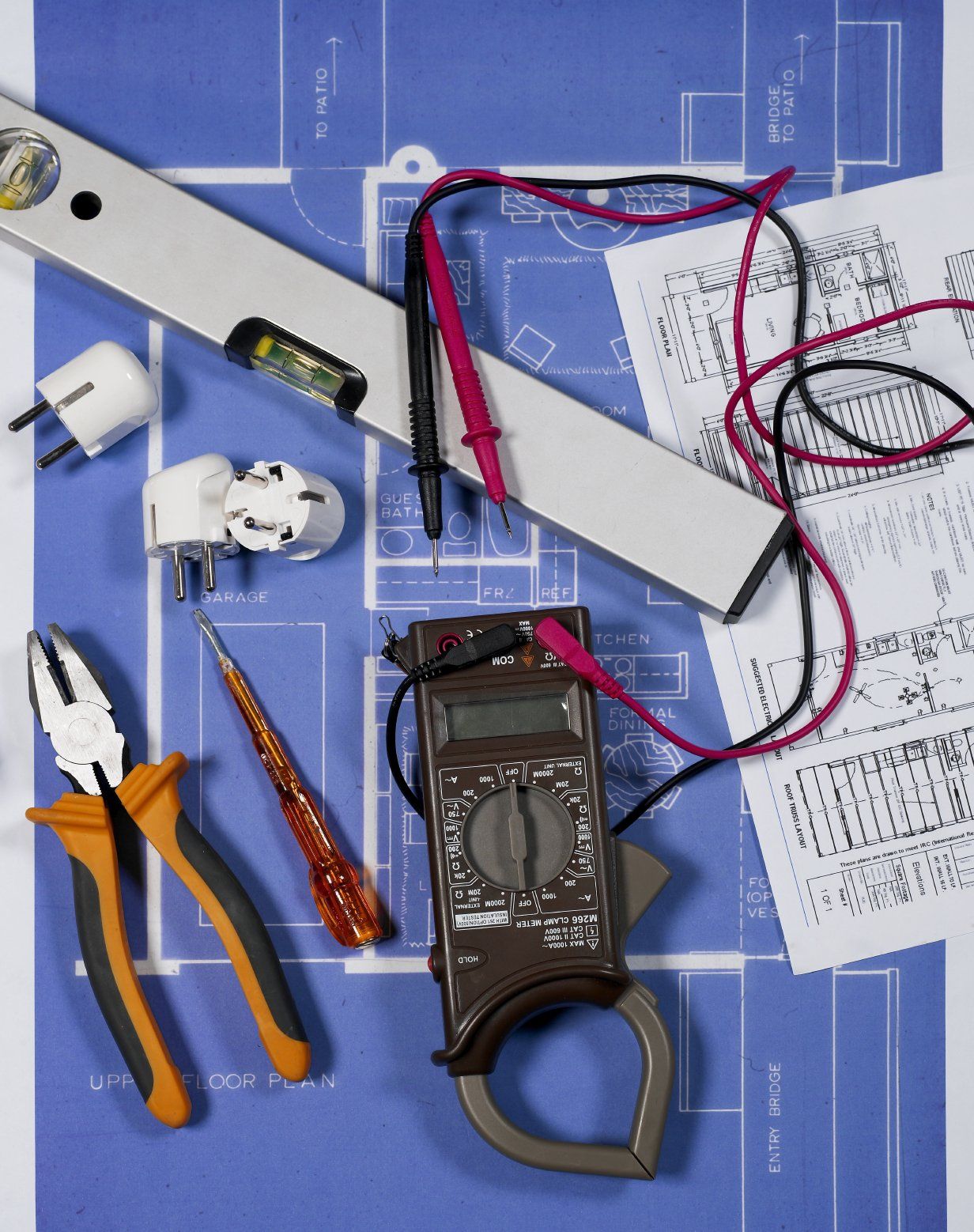
Definition of Total Productive Maintenance (TPM)
Total Productive Maintenance (TPM) is a comprehensive and proactive maintenance strategy that focuses on improving the overall efficiency and effectiveness of manufacturing equipment through the active involvement of all employees. TPM aims to maximise equipment uptime, enhance productivity, and reduce operational costs by integrating maintenance activities into daily operations and promoting a culture of continuous improvement.
Key Objectives of TPM:
- Maximise Equipment Availability: Ensure that equipment is available for production when needed and minimise unplanned downtime
- Enhance Equipment Performance: Improve the performance of equipment by optimising its operating conditions and efficiency
- Increase Product Quality: Reduce defects and improve the quality of products through better equipment performance and reliability
- Reduce Maintenance Costs: Minimise the costs associated with maintenance activities by preventing breakdowns and optimising resource usage
- Engage All Employees: Foster a sense of ownership and responsibility for equipment maintenance among all employees, from operators to management
Core Principles of TPM:
- Autonomous Maintenance: Empowering operators to take ownership of routine maintenance tasks such as cleaning, lubrication, and minor adjustments. This helps to prevent small issues from escalating into major problems
- Planned Maintenance: Developing and implementing a structured maintenance schedule based on predictive and preventive approaches to address potential issues before they lead to equipment failure
- Quality Maintenance: Focusing on maintaining and improving equipment to ensure that it produces high-quality products consistently. This involves identifying and addressing the root causes of quality issues related to equipment performance
- Focused Improvement: Targeting specific areas for improvement based on data analysis and performance metrics. This principle emphasises continuous improvement efforts to address chronic issues and enhance overall equipment effectiveness
- Early Equipment Management: Involving maintenance and operations teams in the design and procurement phases of new equipment to ensure that it meets maintenance and operational requirements
- Training and Education: Providing ongoing training and development opportunities for employees to enhance their skills and knowledge related to equipment maintenance and operation
- Safety, Health, and Environment: Ensuring maintenance practices contribute to a safe and healthy working environment while minimising environmental impact
Software:
In today's market, a variety of sophisticated software solutions are available to help companies manage Total Productive Maintenance (TPM) effectively. These tools are designed to streamline maintenance processes, enhance equipment reliability, and foster a culture of continuous improvement. Leading software options include IBM Maximo, which offers comprehensive asset management and maintenance capabilities, and SAP PM (Plant Maintenance), a robust module within the SAP ERP system that facilitates planning, scheduling, and executing maintenance activities. Additionally, Fiix by Rockwell Automation provides a user-friendly cloud-based platform that integrates with IoT devices to predict maintenance needs and optimise workflows. Another notable solution is UpKeep, known for its mobile-first approach, enabling maintenance teams to manage tasks on the go and respond quickly to issues. These software solutions not only improve the efficiency of TPM but also provide valuable data insights that help organisations make informed decisions and continuously improve their maintenance practices.
By implementing TPM, organisations can achieve significant improvements in equipment performance, production efficiency, and overall operational effectiveness. TPM fosters a culture of continuous improvement and proactive maintenance, which ultimately leads to better business outcomes and enhanced competitiveness.
What is meant by Total Productive Maintenance?
Total Productive Maintenance (TPM) is a proactive approach to equipment and machinery upkeep that aims to prevent breakdowns and boost overall productivity.
Rather than simply fixing problems as they arise, TPM encourages everyone on the team – from top management to operators on the shop floor – to be involved in maintaining machinery and processes, resulting in fewer unplanned stops, higher product quality, and a safer working environment.
Which are the 8 pillars of TPM?
TPM is built around eight key pillars, each focusing on a different aspect of continuous improvement and reliability:
- Focused Improvement – Targeted, small-step improvements that add up to large-scale gains.
- Autonomous Maintenance – Operators take ownership of basic maintenance tasks like cleaning, lubricating, and inspection.
- Planned Maintenance – Scheduled, preventative tasks to avoid unexpected breakdowns.
- Quality Maintenance – Building quality into processes to prevent defects before they occur.
- Early Equipment Management – Designing equipment and processes with efficiency and maintainability in mind.
- Education and Training – Equipping all team members with the knowledge and skills to maintain and improve machinery.
- Office TPM – Extending TPM principles to administrative and support functions for improved overall workflow.
- Safety, Health, and Environment – Ensuring safe working conditions and environmentally friendly processes.
What are the 5 principles of TPM?
Although TPM typically revolves around the eight pillars, you’ll often hear about five foundational principles that underpin its success:
- No Unplanned Downtime – Prevent breakdowns by carefully monitoring and maintaining equipment.
- No Small Stops or Slow Running – Address minor issues immediately before they escalate into bigger problems.
- No Defects – Focus on root cause analysis and error proofing (poka-yoke) to eliminate defects entirely.
- No Accidents – Create a safety-first culture, ensuring everyone follows protocols and best practices.
- No Wasted Resources – Optimise materials, labour, and equipment usage to cut costs and boost efficiency.
What is the difference between TPM and OEE?
TPM (Total Productive Maintenance) is a holistic framework that aims to involve the entire organisation in equipment maintenance and process improvement.
OEE (Overall Equipment Effectiveness) is a specific metric used to measure how effectively equipment is utilised.
It looks at three main factors:
- Availability (the ratio of planned production time that’s actually used for production)
- Performance (how closely machines run to their maximum speed)
- Quality (the proportion of good parts produced without defects)
In simpler terms, TPM is the set of strategies to improve equipment and processes, whereas OEE is a way of measuring how effectively those strategies are working.
Together, they give a powerful way to continuously improve productivity.
Why TPM Matters in Lean Six Sigma
TPM is a cornerstone of a Lean Six Sigma environment because it helps eliminate waste, reduce defects, and streamline processes. By combining the problem-solving rigour of Six Sigma with TPM’s focus on proactive upkeep, organisations can achieve significant boosts in operational excellence.
If you have any further questions about implementing Total Productive Maintenance in your workplace, feel free to ask!
Frequently Asked Questions about Total Productive Maintenance (TPM)
Ask us about TPM
Top Lean Six Sigma Reads:
