ISO 9001 vs. Six Sigma: Enhancing Your QMS with Lean Six Sigma | VA Innovation
Understanding the Difference Between ISO 9001 and Six Sigma: How Lean Six Sigma Enhances Your Quality Management System
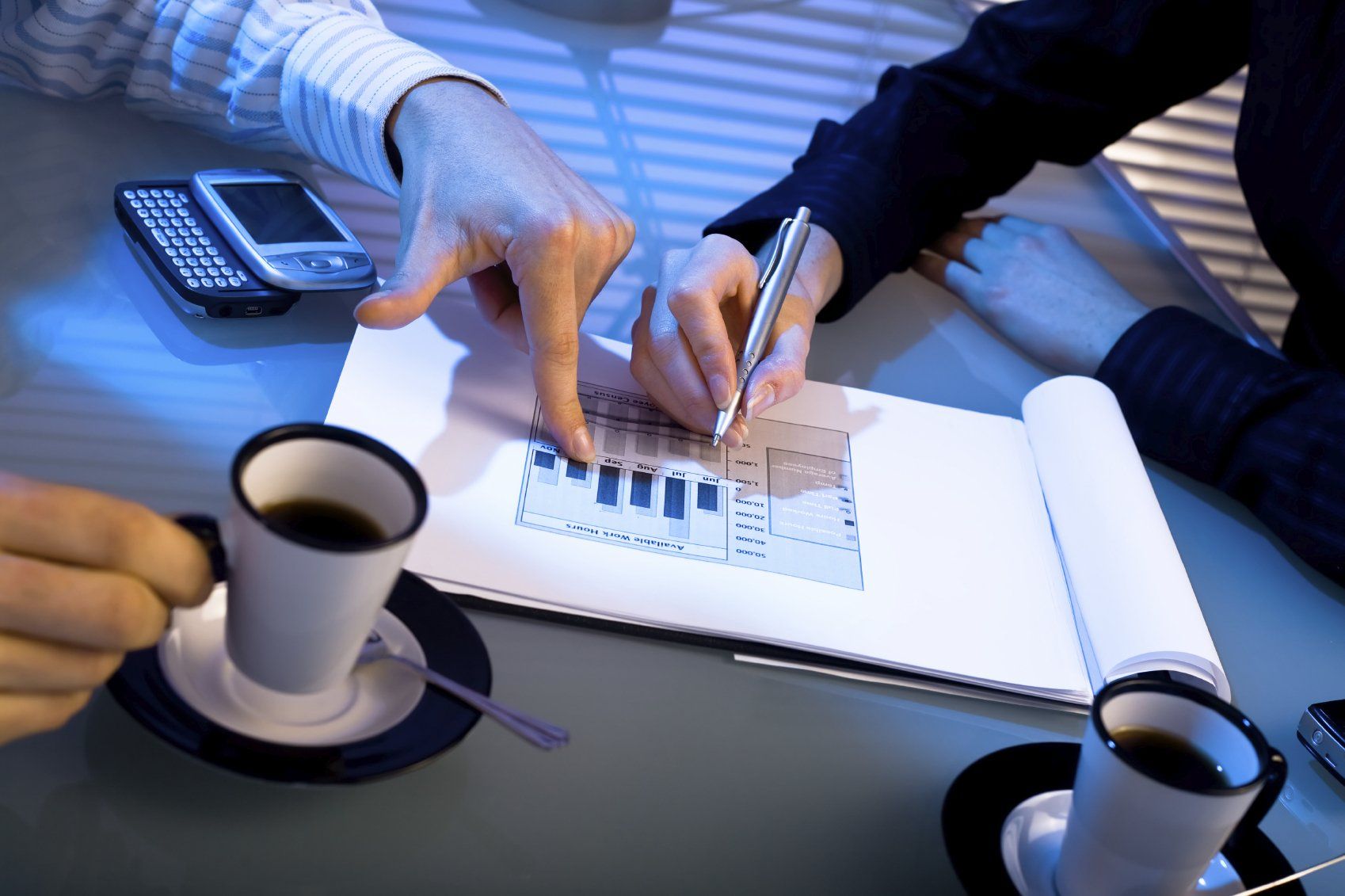
In today's competitive business environment, maintaining a high standard of quality is crucial for success. Two of the most recognised methodologies for quality management are ISO 9001 and Six Sigma. While both aim to improve quality and efficiency, they differ in approach and implementation. This blog post will explore these differences and explain how integrating Lean Six Sigma can significantly enhance your Quality Management System (QMS).
ISO 9001: The Standard for Quality Management
ISO 9001 is an internationally recognised standard for Quality Management Systems (QMS). It provides a framework for organisations to ensure they meet customer and regulatory requirements while continually improving their processes.
Key components of ISO 9001 include:
- Customer Focus: Ensuring that customer needs and expectations are met
- Leadership: Establishing strong leadership to create a unified purpose and direction
- Process Approach: Managing activities as processes that function together as a system
- Continuous Improvement: Emphasising the ongoing improvement of products, services, and processes
- Evidence-Based Decision Making: Using data and analysis to guide decisions
ISO 9001 is often viewed as a broad framework that any organisation can adopt to enhance its quality management practices.
Six Sigma: A Data-Driven Approach to Quality Improvement
Six Sigma, on the other hand, is a methodology focused on reducing variability and defects within processes. It uses statistical tools and techniques to identify and eliminate the root causes of defects and inefficiencies.
The main principles of Six Sigma include:
- Define: Identifying the problem or project goals
- Measure: Collecting data to understand current performance
- Analyse: Identifying the root causes of defects
- Improve: Implementing solutions to address root causes
- Control: Monitoring the process to ensure sustained improvements
Six Sigma is highly data-driven and focuses on achieving quantifiable financial returns by reducing process variation and defects. Find out the nuances of how to properly budget for the cost of LSS here.
Lean Six Sigma: The Best of Both Worlds
Lean Six Sigma combines the principles of Lean (which focuses on reducing waste and improving flow) with the data-driven approach of Six Sigma.
This hybrid methodology provides a powerful toolset for organisations looking to enhance their QMS. Read how McDonalds have utilised the approach here.
How Lean Six Sigma Supports and Improves Your QMS
- Enhanced Process Efficiency: Lean Six Sigma helps identify and eliminate non-value-added activities (waste) in your processes, leading to more efficient operations
- Improved Quality and Consistency: By reducing process variation and defects, Lean Six Sigma ensures more consistent quality, aligning with the objectives of ISO 9001
- Data-Driven Decision-making: Lean Six Sigma’s emphasis on data and statistical analysis complements ISO 9001’s requirement for evidence-based decision-making
- Customer Satisfaction: Both methodologies focus on meeting customer needs and expectations. Lean Six Sigma projects often result in improved customer satisfaction by enhancing product quality and reducing lead times
- Continuous Improvement Culture: Integrating Lean Six Sigma fosters a culture of continuous improvement, essential for maintaining and improving a QMS
- Comprehensive Problem Solving: The structured problem-solving approach of Lean Six Sigma (DMAIC) provides a clear framework for addressing quality issues systematically
- Employee Engagement: Lean Six Sigma encourages involvement and input from all levels of the organisation, promoting a collaborative environment where employees are engaged in improving processes
The Benefits of Being ISO 9001:2015 Certified
Achieving ISO 9001:2015 certification brings a multitude of benefits to an organisation. This certification demonstrates a commitment to quality and continuous improvement, enhancing the organisation's credibility and reputation in the market. It ensures that robust quality management practices are in place, leading to increased efficiency and reduced waste. ISO 9001:2015 helps in meeting regulatory and customer requirements consistently, which can lead to higher customer satisfaction and loyalty.
Additionally, the certification process involves rigorous internal and external audits, fostering a culture of continuous improvement and employee engagement. Ultimately, being ISO 9001:2015 certified can open up new market opportunities, as many customers and partners prefer or even require doing business with certified organisations.
How to Get ISO 9001:2015 Certified
Achieving ISO 9001:2015 certification involves several key steps that ensure an organisation meets the stringent requirements of the standard.
The process begins with a thorough understanding of the ISO 9001:2015 requirements and conducting a gap analysis to identify areas needing improvement.
Next, the organisation must develop or update its Quality Management System (QMS) documentation, including policies, procedures, and process maps, to align with ISO standards. Training employees on the QMS and their roles within it is crucial for effective implementation.
Once the QMS is in place, internal audits are conducted to verify compliance and readiness for the certification audit. The final step is to engage an accredited certification body to perform the external audit, which includes a thorough review of the QMS documentation and its implementation.
Upon successful completion of the audit, the organisation receives ISO 9001:2015 certification, demonstrating its commitment to quality management and continuous improvement.
ISO 9001:2015 Certification Checklist
- Understand ISO 9001:2015 Requirements
- Obtain the ISO 9001:2015 standard.
- Review and understand the requirements and clauses.
- Conduct a Gap Analysis
- Compare existing QMS against ISO 9001:2015 requirements
- Identify gaps and areas needing improvement.
- Develop or Update Quality Management System (QMS) Documentation
- Quality Policy
- Quality Objectives
- Process Maps and Flowcharts
- Procedures and Work Instructions
- Records and Forms
- Management Commitment
- Ensure top management commitment to ISO 9001:2015
- Define roles, responsibilities, and authorities
- Resource Management
- Allocate necessary resources (personnel, training, infrastructure)
- Ensure competence and awareness of employees
- Implementation of QMS
- Implement documented procedures and processes
- Communicate QMS policies and procedures to all employees
- Training and Awareness
- Train employees on ISO 9001:2015 requirements
- Ensure employees understand their roles within the QMS
- Internal Audits
- Plan and conduct internal audits to verify QMS implementation
- Identify non-conformities and implement corrective actions
- Management Review
- Conduct regular management reviews to evaluate QMS performance
- Review quality objectives, audit results, and customer feedback
- Corrective Actions
- Identify root causes of non-conformities
- Implement corrective actions to prevent recurrence
- Select a Certification Body
- Choose an accredited certification body
- Schedule the certification audit
- Pre-Assessment Audit (Optional)
- Conduct a pre-assessment audit to identify any remaining issues
- Address any findings before the official certification audit
- Certification Audit
- Stage 1: Documentation review by the certification body
- Stage 2: On-site audit to assess implementation and effectiveness
- Address Audit Findings
- Address any non-conformities identified during the certification audit
- Implement corrective actions and provide evidence to the certification body
- Receive Certification
- Upon successful completion of the audit, receive ISO 9001:2015 certification
- Maintain and continually improve the QMS.
- Surveillance Audits
- Prepare for regular surveillance audits by the certification body
- Ensure ongoing compliance with ISO 9001:2015 requirements
Incorporating Lean Six Sigma into your Quality Management System can significantly elevate your organisation's performance by marrying the systematic framework of ISO 9001 with the data-driven approach of Six Sigma. This integration not only enhances process efficiency and product quality but also fosters a culture of continuous improvement and customer satisfaction. At VA Innovation, we are committed to guiding you through the complexities of quality management, ensuring you reap the full benefits of these powerful methodologies. Embrace Lean Six Sigma with VA Innovation and transform your QMS into a robust engine for sustained excellence and growth.
Contact us today to learn how we can support your quality management initiatives and drive continuous improvement across your organisation.
Top Lean Six Sigma Reads:
